Medicare GmbH
Fallstudie: Schaftadapter
Daimler AG, BASF SE
Streckgrenzenprüfung Catamold® EVO 316-L
In der Zusammenarbeit von Daimler AG, BASF SE und AIM3D GmbH wurden die Eigenschaften der mittels CEM-Verfahren gedruckten Bauteile eingehend untersucht.
In den Untersuchungen wurden die mechanischen Eigenschaften gedruckter Bauteile aus dem Serienmaterial Catamold® EVO 316-L mit den Eigenschaften konventioneller Metallspritzgussteile (MIM) aus dem gleichen Material verglichen. Sowohl die Dichtewerte nach dem Sintern als auch die ermittelten Festigkeiten zeigen, dass die Eigenschaften der 3D-gedruckten Bauteile mit den Eigenschaften der Serienfertigung vergleichbar sind.
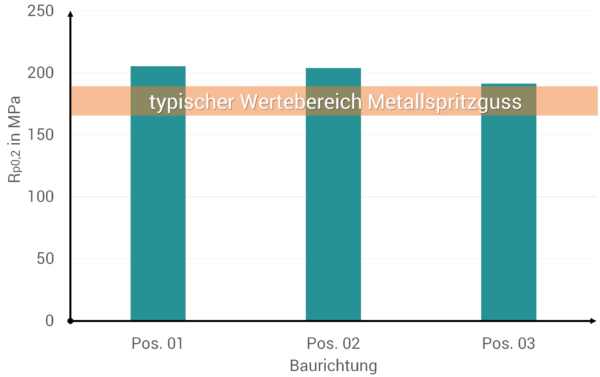
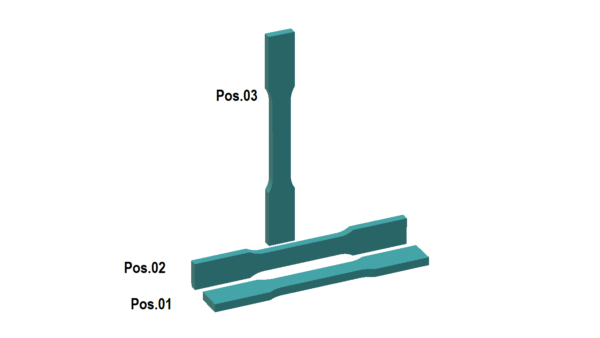
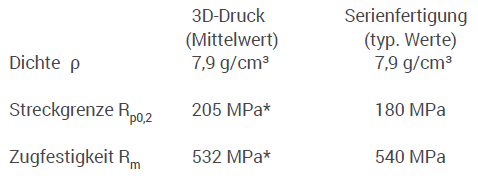
*Werte: “Kopp, Alexander: Potenzialermittlung von Additiven Fertigungsverfahren (3D-Drucken) für metallische Fahrzeugstrukturbauteile in der Serienproduktion [voraussichtlicher Titel], unveröffentlichte und noch nicht abgeschlossene Masterarbeit, Universität Stuttgart/ Daimler AG, 2018”
Schunk Sintermetalltechnik GmbH
Prüfungsversuch: Zugstab aus HK 30
Die Übertragbarkeit der Materialeigenschaften von 3D-gedruckten Teilen spielt eine essenzielle Rolle bei der Ergänzung bestehender Produktionsketten. Um dies zu beurteilen, wurde ein HK 30 der Firma Schunk Sintermetalltechnik im 3D Druck verarbeitet untersucht.
HK 30 ist ein Stahl für Hochtemperaturanwendungen. Der Werkstoff kann bei bis zu 850°C eingesetzt werden. Ein typischer Anwendungsbereich ist die Automobilbranche wo das Material beispielsweise für Anwendungen in Turboladern eingesetzt wird.
Dichtebestimmung DIN EN ISO 3369
AIM3D | 7,54 g/cm³ |
Soll lt. Werkstoffdatenblatt | ≥ 7,50 g/cm3 |
In den Ergebnissen der Dichtebestimmung ist zu erkennen, dass der Zugstab, welcher mit dem CEM-Verfahren gedruckt wurde, den Anforderungen laut dem Werkstoffdatenblatt entspricht.
Zugversuch DIN EN ISO 6892-1 A
Streckgrenze / Dehngrenze Rp0,2 [MPa] | Zugfestigkeit Rm [MPa] | Bruchdehnung L0=20mm A [%] | |
AIM3D | 363 | 722 | 26,8 |
Soll lt. Werkstoffdatenblatt | > 350 | > 650 | > 20 |
Oberflächenhärtegrade / Kernhärte DIN EN ISO 6507-1
Es wurde ebenfalls die Oberflächenhärtegrade und die Kernhärte nach der DIN EN ISO 6507-1 gemessen. Die Prüfwerte wurden mit dem Werkstoffdatenblatt verglichen und haben ein überdurchschnittliches Ergebnis erreicht. Der Mittelwert der durchgeführten Versuche lag bei 199 bzw. 213.
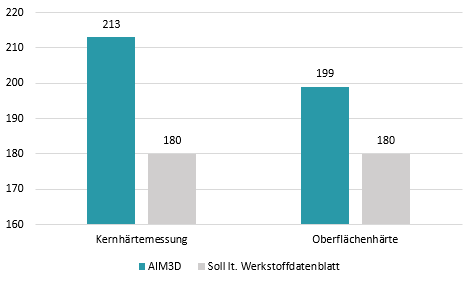
Zusammenfassend kann festgestellt werden, dass die Prüfungen erfolgreich durchgeführt werden konnten. In allen Test hat sich das CEM-Verfahren der AIM3D GmbH bewiesen und kann somit mit klassischen Fertigungsverfahren konkurrieren.
Alle Testergebnisse wurden von der Schunk Sintermetalltechnik GmbH, Prüflabor “Friedrich Eisenkolb” durchgeführt. Bericht Nr. 190393 vom 22.02.2019